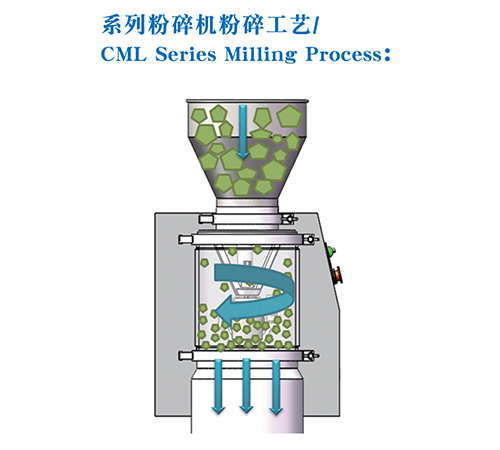
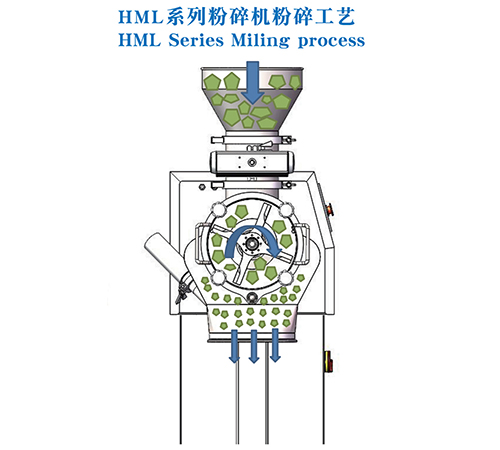
शंकु मिलिंग
शंकु मिलों, या शंक्वाकार स्क्रीन मिलों का उपयोग पारंपरिक रूप से फार्मास्युटिकल सामग्री के आकार को एक समान तरीके से कम करने के लिए किया जाता रहा है। हालाँकि, इनका उपयोग मिश्रण, छानने और फैलाव के लिए भी किया जा सकता है। वे विभिन्न आकारों में आते हैं, जिनमें टेबलटॉप प्रयोगशाला उपकरणों से लेकर बड़े पैमाने पर, बड़े फार्मास्युटिकल प्रसंस्करण कार्यों के लिए उपयोग की जाने वाली उच्च क्षमता वाली मशीनें शामिल हैं।
जबकि शंकु मिलों का उपयोग अलग-अलग होता है, फार्मास्यूटिकल्स में उनका उपयोग करने की प्रवृत्ति में उत्पादन के दौरान सूखे पदार्थों को डी-लंपिंग करना शामिल है; सुखाने से पहले गीले दानेदार कणों को आकार देना; और सूखे दानेदार कणों को सूखने के बाद और टेबलेट बनाने से पहले उनका आकार निर्धारण करना।
अन्य मिलिंग तकनीकों की तुलना में, कोन मिल दवा निर्माताओं को अन्य विशिष्ट लाभ भी प्रदान करती है। इन लाभों में कम शोर, अधिक समान कण आकार, डिज़ाइन लचीलापन और उच्च क्षमता शामिल हैं।
आज बाजार में सबसे नवीन मिलिंग तकनीक अधिक थ्रूपुट और उत्पाद आकार वितरण प्रदान करती है। इसके अलावा, वे परिवर्तनीय छलनी (स्क्रीन) और प्ररित करनेवाला विकल्पों के साथ उपलब्ध हैं। जब कम घनत्व वाली सामग्रियों के साथ उपयोग किया जाता है, तो एक छलनी सीधी सलाखों के साथ डिज़ाइन की गई मिलों की तुलना में थ्रूपुट को 50 प्रतिशत से अधिक बढ़ा सकती है। कुछ मामलों में, उपयोगकर्ताओं ने प्रति घंटे 3 टन तक की इकाई उत्पादन क्षमता हासिल कर ली है।
धूल रहित शंकु मिलिंग प्राप्त करना
यह सर्वविदित है कि मिलिंग से धूल उत्पन्न होती है, जो विशेष रूप से ऑपरेटरों और फार्मास्युटिकल प्रसंस्करण पर्यावरण के लिए खतरनाक हो सकती है यदि धूल को नियंत्रित नहीं किया जाता है। धूल की रोकथाम के लिए कई विधियाँ उपलब्ध हैं।
बिन-टू-बिन मिलिंग एक पूरी तरह से इन-लाइन प्रक्रिया है जो शंकु मिल के माध्यम से सामग्री को खिलाने के लिए गुरुत्वाकर्षण पर निर्भर करती है। तकनीशियन मिल के नीचे एक बिन रखते हैं, और मिल के ठीक ऊपर रखा गया एक बिन मिल में सामग्री छोड़ता है। गुरुत्वाकर्षण मिलिंग के बाद सामग्री को सीधे निचले कंटेनर में जाने की अनुमति देता है। यह उत्पाद को शुरू से अंत तक समाहित रखता है, साथ ही मिलिंग के बाद सामग्री को स्थानांतरित करना आसान बनाता है।
एक अन्य विधि वैक्यूम ट्रांसफर है, जो एक इन-लाइन प्रक्रिया भी है। इस प्रक्रिया में धूल शामिल है और ग्राहकों को उच्च दक्षता और लागत बचत प्राप्त करने में मदद करने के लिए प्रक्रिया को स्वचालित भी किया गया है। इन-लाइन वैक्यूम ट्रांसफर सिस्टम का उपयोग करके, तकनीशियन शंकु की ढलान के माध्यम से सामग्री को खिला सकते हैं और उन्हें मिल के आउटलेट से स्वचालित रूप से खींच सकते हैं। इस प्रकार, शुरू से अंत तक, प्रक्रिया पूरी तरह से संलग्न है।
अंत में, आइसोलेटर मिलिंग में मिलिंग के दौरान महीन पाउडर शामिल करने की सिफारिश की जाती है। इस विधि के साथ, शंकु मिल एक दीवार फिक्सिंग फ्लैंज के माध्यम से एक आइसोलेटर के साथ एकीकृत होता है। शंकु मिल का निकला हुआ किनारा और विन्यास आइसोलेटर के बाहर प्रसंस्करण क्षेत्र द्वारा शंकु मिल हेड के भौतिक विभाजन की अनुमति देता है। यह कॉन्फ़िगरेशन ग्लोव बॉक्स के माध्यम से आइसोलेटर के अंदर किसी भी सफाई को करने की अनुमति देता है। यह धूल के जोखिम को कम करता है और प्रसंस्करण लाइन के अन्य क्षेत्रों में धूल के स्थानांतरण को रोकता है।
हथौड़ा मिलिंग
हैमर मिलें, जिन्हें कुछ दवा प्रसंस्करण निर्माताओं द्वारा टर्बो मिल भी कहा जाता है, आमतौर पर अनुसंधान और उत्पाद विकास के साथ-साथ निरंतर या बैच उत्पादन के लिए उपयुक्त हैं। इन्हें अक्सर ऐसे मामलों में नियोजित किया जाता है जहां दवा डेवलपर्स को कठिन-से-मिल एपीआई और अन्य पदार्थों की सटीक कण कटौती की आवश्यकता होती है। इसके अलावा, हथौड़ा मिलों का उपयोग टूटी हुई गोलियों को पाउडर में पीसकर सुधार के लिए पुनः प्राप्त करने के लिए किया जा सकता है।
उदाहरण के लिए, निरीक्षण करने पर, कुछ निर्मित टैबलेट कई कारणों से ग्राहक के मानकों के अनुरूप नहीं हो सकते हैं: गलत कठोरता, खराब उपस्थिति, और अधिक या कम वजन। उन मामलों में, निर्माता सामग्री पर नुकसान उठाने के बजाय गोलियों को वापस उनके पाउडर के रूप में मिलाने का विकल्प चुन सकता है। गोलियों को दोबारा मिल कर उत्पादन में वापस लाने से अंततः बर्बादी कम होती है और उत्पादकता बढ़ती है। लगभग सभी स्थितियों में जहां टैबलेट का एक बैच विनिर्देशों को पूरा नहीं करता है, निर्माता समस्या को दूर करने के लिए हैमर मिल का उपयोग कर सकते हैं।
हैमर मिलें प्रति घंटे 1,500 किलोग्राम तक उत्पादन करते हुए 1,000 आरपीएम से 6,000 आरपीएम तक की गति से काम करने में सक्षम हैं। इसे प्राप्त करने के लिए, कुछ मिलें एक स्वचालित घूर्णन वाल्व से सुसज्जित होती हैं जो तकनीशियनों को मिलिंग कक्ष को बिना ओवरफिलिंग के सामग्री के साथ समान रूप से भरने की अनुमति देती है। ओवरफिल को रोकने के अलावा, ऐसे स्वचालित फीडिंग उपकरण प्रक्रिया की पुनरावृत्ति को बढ़ाने और गर्मी उत्पादन को कम करने के लिए मिलिंग कक्ष में पाउडर के प्रवाह को नियंत्रित कर सकते हैं।
कुछ अधिक उन्नत हथौड़ा मिलों में दो तरफा ब्लेड असेंबली होती है जो गीली या सूखी सामग्री की व्यवहार्यता को बढ़ाती है। ब्लेड का एक किनारा सूखी सामग्री को तोड़ने के लिए हथौड़े की तरह काम करता है, जबकि चाकू जैसा हिस्सा गीली सामग्री को काट सकता है। उपयोगकर्ता बस उन सामग्रियों के आधार पर रोटर को फ्लिप करते हैं जिन्हें वे मिल रहे हैं। इसके अतिरिक्त, कुछ मिल रोटर असेंबलियों को विशिष्ट उत्पाद व्यवहार के लिए समायोजित करने के लिए उलटा किया जा सकता है, जबकि मिल का रोटेशन अपरिवर्तित रहता है।
कुछ हथौड़ा मिलों के लिए, कण का आकार मिल के लिए चुने गए स्क्रीन आकार के आधार पर निर्धारित किया जाता है। आधुनिक हथौड़ा मिलें सामग्री के आकार को 0.2 मिमी से 3 मिमी तक कम कर सकती हैं। एक बार प्रसंस्करण पूरा हो जाने पर, मिल स्क्रीन के माध्यम से कणों को धकेलती है, जो उत्पाद के आकार को नियंत्रित करती है। अंतिम उत्पाद का आकार निर्धारित करने के लिए ब्लेड और स्क्रीन मिलकर काम करते हैं।
पोस्ट करने का समय: अगस्त-08-2022